- Learning and Development
A Guide to Manufacturing Training Videos
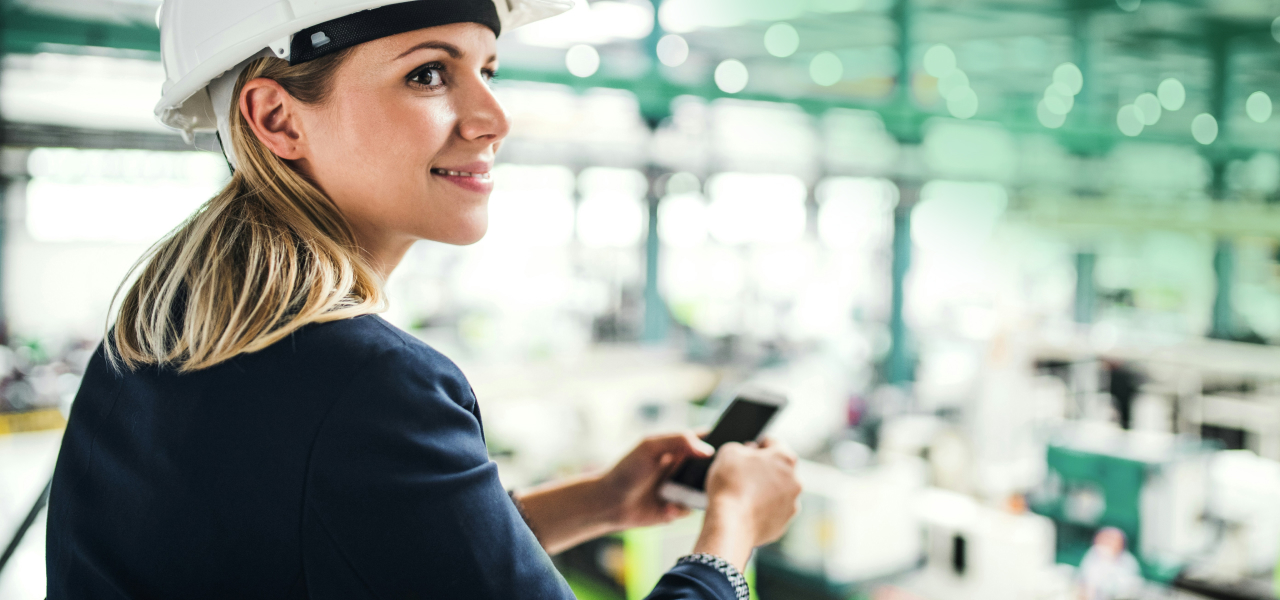
Video is a powerful tool for training, and its use has grown rapidly in recent years. It is an increasingly important medium for manufacturing companies to engage their employees in training. Video training is also instrumental to a company’s revenue, with The Educators reporting that 42% of companies using video for training are seeing an increase in income.
Video plays an increasingly critical role in modern manufacturing communication and training. There are several ways in which video can enhance employee learning and development. From creating product demonstrations to offering virtual tours of facilities, video helps companies build a more knowledgeable, skilled, and productive workforce.
In this guide, you’ll learn:
- Seven Ways Manufacturing Companies Use Video for Training
- Benefits of Using Video for Manufacturers
- How is video being used to improve manufacturing operations?
- What are the obstacles to training manufacturing employees?
- How to Effectively Train Manufacturing Workers
- How to empower manufacturing employees
- Best practices for training manufacturing workers with video
- The Future of Manufacturing Training
How Manufacturing Companies Use Video for Training
Video allows companies to create engaging and interactive learning experiences and standardize training procedures across different locations.
According to the Research Institute of America, Video-based training has increased retention rates by 25-60% compared to traditional training methods.
Seven ways manufacturers train with video.
- Demonstrating proper use of equipment and machinery
- Presenting product knowledge and information
- Providing step-by-step instructions for processes and procedures
- Sharing best practices and safety tips
- Conducting virtual job shadowing or on-the-job training
- Offering continuous learning and skill development opportunities
- Providing onboarding and orientation for new hires.
Benefits of using video for manufacturers.
Manufacturers can greatly benefit from using video for training, communicating with, and onboarding their employees. These benefits include:
- Increasing operational efficiency
- Creating a positive company culture
- Increasing employee satisfaction, retention, and empowerment
- Boosting a company’s status as an ideal employer
- Standardization of training across locations and departments
- Flexibility for employees to access training materials at their own pace
- Enhanced collaboration and communication among employees
- Reduction of training costs compared to traditional in-person training
- Improved overall quality and efficiency of training programs
Additionally, videos can be easily accessed and viewed on-demand, which makes it convenient for employees to refer back to them when they need to refresh their knowledge. By using videos for training, manufacturing companies can improve the efficiency and effectiveness of their training programs, resulting in a better-informed and more skilled workforce.
69% of corporate L&D professionals say companies could improve onboarding with video.
Four ways video improves manufacturing operations.
Sometimes, learning means improving the way you work. Here are five ways video helps you operate.
1. Enhanced visual demonstrations for complex procedures.
Video training visually demonstrates processes, procedures, and techniques that employees easily understand. This helps eliminate misunderstandings of written instructions. Visuals also help retain information and provide a reference point for employees to check.
2. Reducing downtime with video training.
One of the biggest benefits of video training in manufacturing operations is reducing downtime. When employees are trained on a new process or procedure using video, they can see a visual representation of the steps involved, which minimizes the chance of making mistakes. This is especially important in industries where production is time-sensitive and costly, as every minute of downtime can have significant financial consequences.
3. Standardizing safety, compliance, and skills training procedures.
Consistent processes and procedures are crucial in a manufacturing setting. Video training allows for the standardization of safety, compliance, and skills training procedures, ensuring that all employees receive the same information and are taught the same methods. This helps to avoid discrepancies in skills taught and ensures consistency across the production line.
4. Maintaining technological advancements.
The manufacturing industry constantly evolves, with new technologies and techniques developed continuously. Video training provides an efficient and cost-effective way for employees to learn about these advancements, ensuring that the manufacturing operation stays up-to-date and remains competitive in the marketplace.
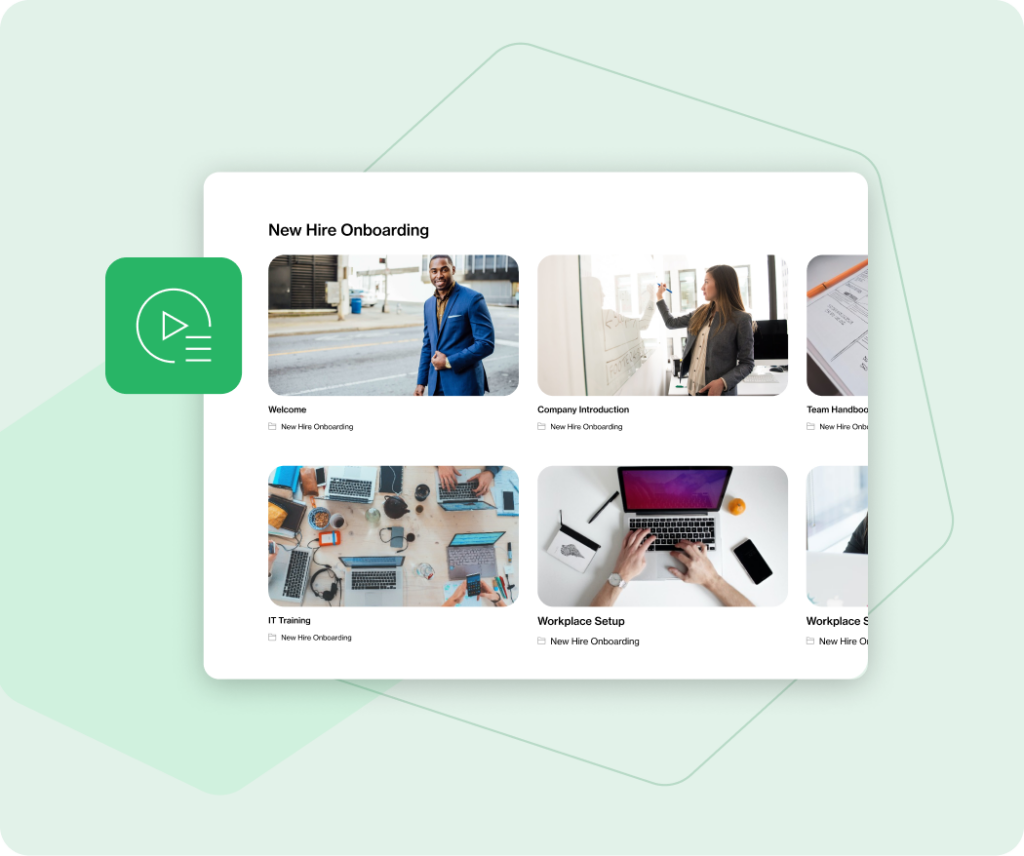
Obstacles to successful manufacturing training.
1. Lack of Time and Resources
One of the biggest obstacles to training manufacturing workers is the lack of time and resources. Manufacturing is a fast-paced, high-pressure environment where every minute counts. Taking workers off the production line for training can decrease productivity and costs. Additionally, many companies do not have the budget or resources to invest in training programs and materials.
2. Resistance to Change
Another challenge is resistance to change. Some workers may resist new training programs and technologies because they are comfortable with how things have always been done. This resistance can be due to fear of the unknown, lack of trust in new systems, or simply not seeing the value in change.
3. Technological Changes
The manufacturing industry constantly evolves, introducing new technologies and processes regularly. Keeping workers trained and up-to-date with these changes can be difficult and time-consuming. Additionally, many workers may not have the technical skills or background to adapt to new technologies easily.
4. High Turnover Rates
High turnover rates can make it difficult to provide ongoing training to workers. When workers are constantly coming and going, it can be challenging to provide consistent training and ensure that all workers are up-to-date on the latest processes and technologies.
5. Limited Availability of Skilled Instructors
Another obstacle is the limited availability of skilled instructors. Finding trainers with the expertise and experience to teach new technologies and processes effectively can be challenging. Additionally, many companies may not have the budget to hire additional trainers or bring in outside experts.
So, what can you do about these obstacles? By focusing on empowering your staff, you can transform your organizational learning into consistent, engaging training that meets your employees’ needs.
8 Ways Manufacturers Put Video to Work
How to Effectively Train Manufacturing Workers
Effectively training manufacturing employees is essential for ensuring a company’s success and competitiveness. Proper training helps workers develop the skills and knowledge they need to perform their jobs efficiently and effectively, resulting in increased productivity and reduced errors.
Well-trained workers are also more likely to be engaged and motivated, leading to lower turnover rates and improved morale. In addition, training helps employees stay up-to-date with the latest processes and technologies, allowing the company to stay ahead of the competition and respond to changes in the market. Effective training also helps build a continuous improvement culture, where workers are encouraged to develop their skills and take on new challenges.
“With Panopto, [employees] have the option to prepare for a course in advance and learn faster. And those unable to participate physically still have the opportunity to benefit.”
Birgitte Wilki, Administrative Coordinator at Group Technonlogy, ROCKWOOL
Three ways to empower manufacturing employees.
Empowering manufacturing workers is vital not only for morale and retention but also for increasing workers’ ability to do their jobs successfully.
1. Communication is key.
Open communication between management and employees can help build workers’ trust and a sense of ownership.
2. Training and professional development.
Providing ongoing training and professional development opportunities can increase workers’ skills and confidence, improving performance and job satisfaction.
3. Recognition and rewards.
Recognizing and rewarding employees for their contributions can boost motivation and create a positive workplace culture. By making employees feel valued, they will be more motivated to perform their best and contribute to the organization’s success.
Best practices for training workers with video.
Video is one tool that can help employees successfully receive recognition, professional development, and open communication. These best practices can guide you to develop consistent, effective video training that strengthens engagement and increases productivity.
1. Create relevant and consistent training with on-demand content.
Video training allows you to create consistent content that is relevant and specific to workers’ tasks and responsibilities. By providing a standardized and repeatable method of learning and delivering information to all employees, video helps ensure that everyone receives the same message and understanding.
2. Incorporate interactive elements to strengthen engagement.
Encourage interactivity by including video quizzes, simulations, and gamification. This helps workers retain information and apply it on the job. A video learning library can also let users personalize their viewing experience and increase interactivity.
3. Provide an accessible learning experience for all employees.
Using a cloud-based platform such as Panopto, make training videos accessible to all workers, regardless of location or work schedule. On-demand learning enables employees to easily digest training anytime, anywhere, whether in an office or on-site. In addition, video offers a greater level of accessibility to workers who can utilize tools like captions or watch videos at a slower or faster speed.
4. Evaluate engagement and track progress.
Did you know that 70% of organizations do not track quantitative training feedback, and 89% rarely measure training ROI against learning outcomes desired by leadership? Evaluate the effectiveness of video training through data and analytics that help companies understand how employees interact with content. This information can be used to make continuous improvements to the training program.
The Future of Manufacturing Training
As technology advances and the need for effective and efficient training increases, manufacturing will continue to embrace video as a flexible and interactive way to deliver training to workers, regardless of location or work schedule.
The advancement of artificial intelligence and machine learning is expected to play a significant role in the future of manufacturing training. Video training platforms that utilize elements of AI can personalize training for each worker, tailoring the content to their learning styles and pace. This can lead to more effective training and improved skills acquisition, ultimately leading to increased productivity and job satisfaction – and Panopto provides the tool to support these endeavors.
Schedule a Panopto demo
Our team will contact you promptly to answer questions and schedule you for a demonstration and a free trial of our video platform.